Unter Aushärtung versteht man chemische Reaktionen, die bei Polymerisationsprozessen ablaufen. Bei Polymerisationsprozessen werden getrennte Moleküle und kürzere Polymerketten miteinander verbunden oder vernetzt, so dass deutlich längere, härtere und steifere Polymerketten entstehen. Während viele Substanzen polymere Strukturen haben, konzentrieren sich Polymerchemie und Polymertechnik hauptsächlich auf Materialien und Prozesse, bei denen Kunststoffe und Kautschuke zum Einsatz kommen.
Über die Schaltflächen unten gelangen Sie direkt zu einem bestimmten Abschnitt.
Wenn Sie Fragen zur hier verwendeten Terminologie haben, können Sie unseren Artikel zur UV-Härtungsterminologie lesen, um mehr zu erfahren.
Unter Aushärtung versteht man chemische Reaktionen, die bei Polymerisationsprozessen ablaufen. Bei Polymerisationsprozessen werden getrennte Moleküle und kürzere Polymerketten miteinander verbunden oder vernetzt, so dass deutlich längere, härtere und steifere Polymerketten entstehen. Während viele Substanzen polymere Strukturen haben, konzentrieren sich Polymerchemie und Polymertechnik hauptsächlich auf Materialien und Prozesse, bei denen Kunststoffe und Kautschuke zum Einsatz kommen.
Die UV-Photopolymerisation, auch Strahlungshärtung oder einfach UV-Härtung genannt, ist eine spezielle Polymerisationskategorie, bei der ultraviolette Energie die Vernetzung in UV-formulierten Materialien wie Tinten, Beschichtungen, Klebstoffen und Extrusionen vorantreibt. Die Technologie wird seit fast einem Dreivierteljahrhundert erfolgreich in verschiedenen Herstellungsprozessen in vielen verschiedenen Branchen eingesetzt. Dies liegt daran, dass die UV-Härtung äußerst wünschenswerte Materialeigenschaften mit Hochgeschwindigkeitsanlagen mit geringer Stellfläche erzeugt, die Materialien, die sich nass anfühlen, sofort und effizient in feste Strukturen umwandeln, die sich trocken anfühlen.
In vielen Anwendungen bestehen UV-Formulierungen aus Feststoffen oder Materialien mit hohem Feststoffgehalt, die keine flüssigen Träger enthalten. Die festen Partikel sind einfach klein genug und zahlreich genug, um auf eine Vielzahl von Oberflächen aufgetragen zu werden, als wären sie Flüssigkeiten. Während Anwender und Industriezulieferer die schnelle Strukturveränderung der UV-Härtung manchmal als Trocknung beschreiben, werden UV-formulierte Tinten, Beschichtungen und Klebstoffe nicht getrocknet. Sie sind geheilt.
Im Gegensatz dazu enthalten herkömmliche Formulierungen auf Wasser- und Lösungsmittelbasis tatsächlich flüssige Träger, deren Hauptzweck darin besteht, das Auftragen des gewünschten Feststoffgehalts auf die vorgesehenen Oberflächen durch verschiedene Druck-, Sprüh-, Beschichtungs- und Abgabemethoden zu erleichtern. Nach dem Auftragen ist die Arbeit des Trägers beendet und er muss verdampft oder mit Umluft- oder Thermotrocknern getrocknet werden. Nach der Verdunstung verbleiben nur die festen Partikel auf der Oberfläche des Teils, Substrats oder der Konstruktion. Im Falle von Lösungsmittelträgern schreiben Vorschriften häufig vor, dass verdampfte Lösungsmitteldampfer nach Brennern eingebrannt werden müssen, bevor sie an die Umwelt abgegeben werden.
Für viele wasser- und lösungsmittelbasierte Prozesse, die kein UV-Licht zum Aushärten nutzen, müssen lange Trockentunnel und energieverbrauchende Öfen in die Produktionslinien integriert werden, um die Verdunstung aktiv voranzutreiben. Im Gegensatz zur UV-Härtung kommt es bei Trocknungsprozessen nicht zu molekularen Veränderungen innerhalb der Chemie. Sie hinterlassen einfach unverbundene Restfeststoffe, die direkt auf der Oberfläche nicht poröser Materialien wie Kunststoff und Metall ruhen oder leicht in poröse Strukturen wie Holz und Papier absorbiert werden. Rückstände von Feststoffen sind oft anfällig für Kratzer, Beschädigungen, Abnutzung, chemische Zerstörung und Witterungseinflüsse. In vielen Fällen müssen bei wasser- und lösungsmittelhaltigen Materialien klare Deckbeschichtungen sowie andere Schutzmechanismen wie eine Folienkaschierung verwendet werden.
Bei der UV-Härtung führen lange Polymerketten und unglaublich starke Molekülstrukturen zu äußerst wünschenswerten physikalischen, mechanischen und ästhetisch ansprechenden Eigenschaften, die letztendlich das Gesamterscheinungsbild, die Qualität und die Leistung zahlreicher Alltagsgegenstände verbessern. Daher wird die UV-Härtung von Herstellern häufig verwendet, um lebendige Tintenfarben zu erzeugen. visuelle, taktile und haptische Spezialeffekte; unglaublich starke Zerstörungsbindungen; überlegene chemische Beständigkeit und Witterungseinflüsse; und wünschenswerte Oberflächenqualitäten wie Härte, Rutschfestigkeit und Schlagfestigkeit. Die UV-Härtung ist umweltfreundlich, da sie energieverbrauchende Öfen und Trockentunnel, flüchtige organische Verbindungen (VOCs) und gefährliche Luftschadstoffe (HAPs) überflüssig macht. Da UV-Härtungsprozesse die chemische Vernetzung in Sekundenbruchteilen vorantreiben und die Reaktion am Ende abgeschlossen ist, sind Nachhärtung, Verarbeitung, Verpackung, Montage, Abfüllung und Versand unmittelbar nach der letzten UV-Härtungsstation möglich.
Lichtwissenschaft
Das elektromagnetische Spektrum stellt die kontinuierliche Reichweite des gesamten Lichts im Universum dar, einschließlich des Lichts, das von Objekten auf der Erde und von Himmelskörpern emittiert wird. Da Licht immer von einer emittierenden Quelle nach außen strahlt, wird es oft als elektromagnetische Strahlung oder einfach als Strahlung bezeichnet. Eine grafische Darstellung des elektromagnetischen Spektrums ist in der folgenden Abbildung dargestellt.
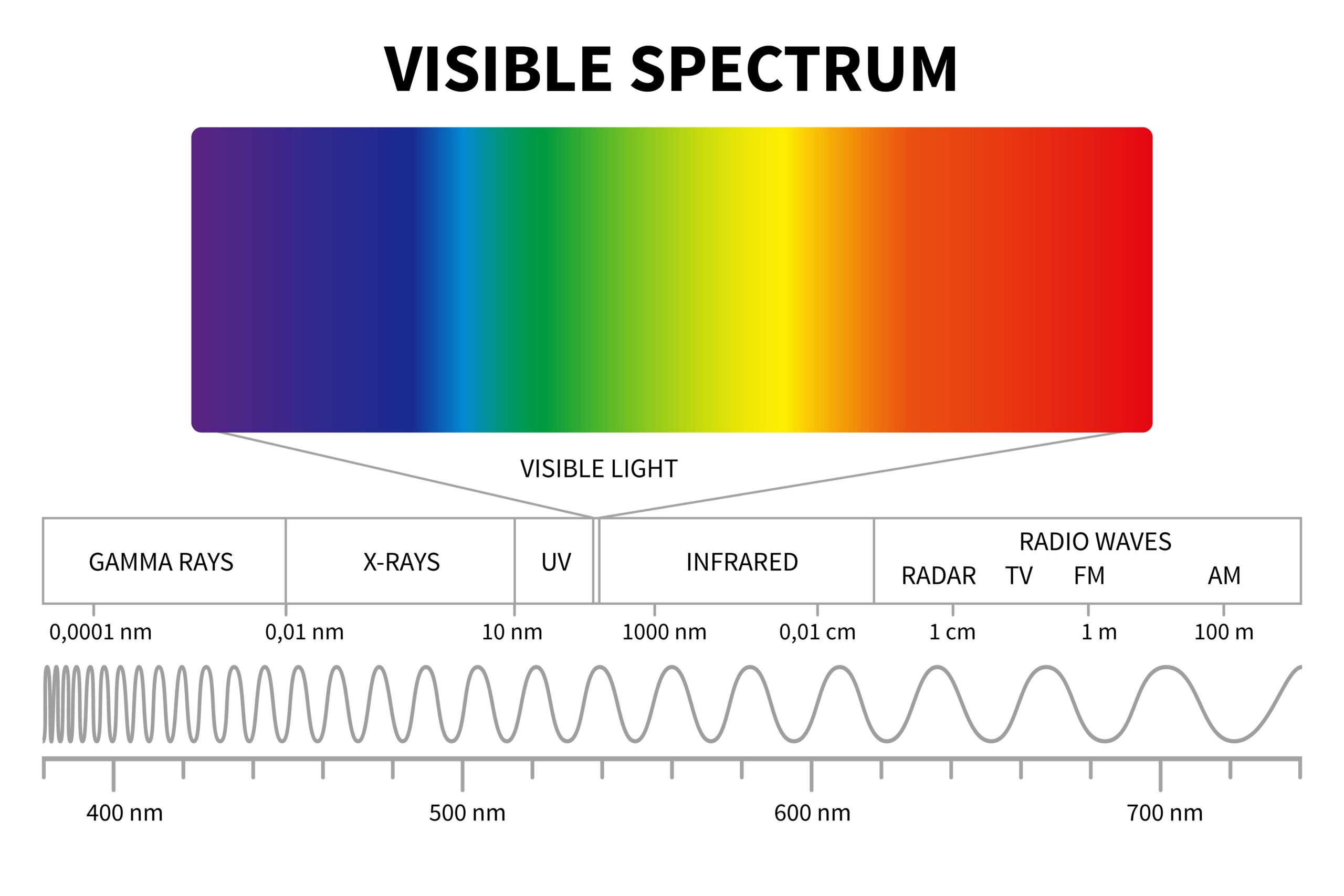
Das elektromagnetische Spektrum ist in Gammastrahlen, Röntgenstrahlen, ultraviolette, sichtbare, Infrarot- und Radiowellen unterteilt. Die ultraviolette Bandbreite wird weiter in Vakuum-UV, UVC, UVB, UVA und UVV unterteilt. Radiowellen werden in Radar-, TV-, FM- und AM-Wellen unterteilt, wobei Mikrowellen als kleineres Untersegment des Radars und häufiger als eigenständiges Band zwischen Infrarot- und Radiowellen unterschieden werden. Jeder Abschnitt im Spektrum wird diskret nach Wellenlänge, Frequenz und photonischer Energie quantifiziert. Mit Ausnahme des sichtbaren Lichts, das bei der Interaktion mit Objekten Farbe erzeugt, ist alles Licht innerhalb des Spektrums unsichtbar.
Die Grenzen zwischen den Lichtbändern sind nicht starr und es gibt keine offiziell festgelegte Wellenlänge, bei der das eine endet und das andere beginnt. Infolgedessen verweisen verschiedene Branchen, Organisationen, Standards und Messinstrumente auf leicht unterschiedliche Bereiche. Für die UV-Härtung werden im Allgemeinen die folgenden Bereiche verwendet.
- Vakuum-UV (100 – 200 nm) – Teil des elektromagnetischen Spektrums zwischen 100 und 200 nm. Vakuum-UV-Wellenlängen werden so genannt, weil sie sich im Vakuum am besten ausbreiten und nicht durch die Luft. Von Härtungssystemen abgegebenes Vakuum-UV ist bei Photopolymerisationsprozessen nur wirksam, wenn UV-Systeme und Härtungsoberflächen in stickstoffinerten Umgebungen betrieben werden. Abhängig von der Sauerstoffkonzentration der inerten Umgebung ist es möglich, dass Vakuum-UV Ozon erzeugt.
- UVC (200 – 280 nm) – Teil des elektromagnetischen Spektrums zwischen 200 und 280 nm. UVC wird allgemein als kurzes UV oder keimtötendes UV bezeichnet und ist für das menschliche Auge unsichtbar. Ozon entsteht im Allgemeinen bei UVC-Wellenlängen von 240 nm und weniger. UVC-Wellenlängen werden an der Oberfläche der UV-Chemie absorbiert und treiben die Oberflächenhärtung voran.
- UVB (280 – 315 nm) – Teil des elektromagnetischen Spektrums zwischen 280 und 315 nm. UVB ist für das menschliche Auge unsichtbar. UVB-Wellenlängen dringen tiefer in die Chemie ein als UVC, jedoch nicht so weit wie UVA und UVV.
- UVA (315 – 400 nm) – Teil des elektromagnetischen Spektrums zwischen 315 und 400 nm. UVA stellt den größten Anteil der UV-Energie dar und wird allgemein als langes UV bezeichnet. UVA liegt an der unteren Grenze dessen, was das menschliche Auge als Farbe wahrnimmt. UVA-Wellenlängen dringen tief in die UV-Chemie ein.
- UVV (400 – 450 nm) – Teil des elektromagnetischen Spektrums zwischen 400 und 450 nm. Das V steht für sichtbar, da diese Wellenlängen vom menschlichen Auge als Farbe wahrgenommen werden und einen kleinen Teil des sichtbaren Spektrums überlappen. UVV-Wellenlängen dringen tief in die UV-Chemie ein.
- Ultraviolett (100 – 450 nm) – Teil des elektromagnetischen Spektrums zwischen 100 und 450 nm. Die Grenze zwischen UV- und sichtbaren Wellenlängen ist nicht genau definiert und wird allgemein als irgendwo zwischen 400 und 450 nm liegend angesehen. UV-Wellenlängen liegen knapp über dem, was das menschliche Auge als Farbe Violett wahrnimmt.
- sichtbar (400 – 700 nm) – Teil des elektromagnetischen Spektrums zwischen 400 und 700 nm. Sichtbares Licht enthält alle Farbtöne, und unterschiedliche Farben werden durch unterschiedliche Wellenlängen oder Kombinationen von Wellenlängen erzeugt, die von Objekten reflektiert werden. Das sichtbare Spektrum wird oft durch einen Regenbogen dargestellt.
- Infrarot (700 nm – 0,1 mm) – Teil des elektromagnetischen Spektrums zwischen 700 nm und 0,1 mm. Infrarotwellenlängen liegen knapp über dem, was das menschliche Auge als Farbe Rot wahrnimmt. Einige Infrarotwellenlängen geben Wärme ab, andere nicht. Infrarotwellenlängen sind der dominierende Faktor bei der von Elektroden- und Mikrowellen-UV-Härtungssystemen abgestrahlten Wärme. Relativ monochromatische UV-LED-Härtungssysteme emittieren kein Infrarot.
- Mikrowelle (0,1 mm – 10 cm) – ein schmales Band zwischen 0,1 mm und 10 cm, das sich am Rande des Radars und des viel breiteren Radiowellenanteils des elektromagnetischen Spektrums befindet. Mikrowellen können genutzt werden, um eine bestimmte Art von UV-Härtungslampe zu betreiben, die in elektrodenlosen oder Mikrowellen-Härtungssystemen verwendet wird.
Während herkömmliche Breitband-UV-Quellen wie Mikrowellen- und Elektrodenbogenlampen UVA, UVB, UVC und UVV sowie sichtbares und infrarotes Licht emittieren, emittieren kommerziell erhältliche LED-Härtungsquellen relativ schmale UVA-Banden, die näher am sichtbaren Bereich liegen (365, 385, 395, und 405 nm). Daher härtet die herkömmlich formulierte Breitspektrum-UV-Chemie im Allgemeinen nicht gut mit UV-LEDs aus und muss neu formuliert werden, um nur mit längeren UVA- und UVV-Wellenlängen auszuhärten. Glücklicherweise entwickeln Tinten-, Beschichtungs- und Klebstoffhersteller die UV-LED-Chemie zunehmend so, dass eine einzige Formulierung sowohl mit LED- als auch mit herkömmlichen Lampen ausgehärtet werden kann. In den kommenden Jahren werden immer mehr Formulierungen auf diese Dual-Cure-Fähigkeit umsteigen und den allmählichen, aber unvermeidlichen Übergang der Branche zur UV-LED-Härtung vorantreiben.
Wellenlänge, Frequenz und photonische Energie
Jeder Abschnitt des elektromagnetischen Spektrums wird diskret nach Wellenlänge, Frequenz und photonischer Energie quantifiziert. Die Wellenlänge ist ein Maß für den Abstand zwischen entsprechenden Punkten auf einer periodischen Lichtwelle. Typischerweise wird es mit dem griechischen Buchstaben Lambda (l) bezeichnet. Die Frequenz ist die Geschwindigkeit, mit der eine bestimmte Wellenlänge auftritt. Sie wird in Zyklen pro Sekunde oder Hertz (Hz) gemessen und typischerweise durch die Buchstaben (f) oder (v) dargestellt. Frequenz und Wellenlänge hängen durch die Lichtgeschwindigkeit zusammen, wobei die Frequenz die Lichtgeschwindigkeit dividiert durch die Wellenlänge ist. Mit zunehmender Wellenlänge nimmt die Frequenz ab. Umgekehrt nimmt die Frequenz zu, wenn die Wellenlängen kürzer werden.
Sowohl die Frequenz als auch die Wellenlänge können zur Berechnung der Energie aller elektromagnetischen Strahlung im Spektrum verwendet werden. Dies wird mithilfe einer der beiden folgenden äquivalenten Formeln erreicht, die als Planck-Einstein-Beziehung bekannt sind.

Wo:
E = Photonenenergie (Joule)
h = Plancksches Wirkungsquantum (Joule·Sekunde)
c = Lichtgeschwindigkeit (Meter pro Sekunde)
λ = Wellenlänge (Meter)
v = Frequenz (Zyklen pro Sekunde)
Gemäß der Planck-Einstein-Beziehung haben kürzere Wellenlängen wie UVC mehr Energie als längere Wellenlängen wie UVA. Im weiteren Sinne haben alle Wellenlängen im ultravioletten Band deutlich mehr Energie als sichtbare, infrarote, Mikrowellen- und Radiowellen, während sie weniger Energie als Röntgen- und Gammastrahlen haben.
Bestrahlungsstärke (W/cm2)
Die Bestrahlungsstärke ist die Strahlungsleistung, die pro Flächeneinheit auf eine Oberfläche trifft. Sie wird in Watt oder Milliwatt pro Quadratzentimeter (W/cm2 oder mW/cm2) ausgedrückt. Andere häufig verwendete Begriffe für die Bestrahlungsstärke sind Leistungsdichte und Wattdichte. Obwohl technisch inkorrekt, wird die Bestrahlungsstärke allgemein als Intensität bezeichnet, und wann immer von Intensität die Rede ist, wird darunter im Allgemeinen die Bestrahlungsstärke verstanden. Die Bestrahlungsstärke wird typischerweise als höchster Spitzenwert über einen weiten Bereich ultravioletter Wellenlängen oder als Spitzenwerte innerhalb jedes der engeren Segmente von UVC, UVB, UVA und UVV gemessen und angegeben. Die Bestrahlungsstärke sollte sich immer auf das zur Messung verwendete Radiometer sowie auf den Standort des Radiometers in Bezug auf die UV-Quelle beziehen.
Für einen definierten Abstand zwischen einer Härtungsoberfläche und einem UV-Härtungssystem ist die Bestrahlungsstärke für jede Lampenleistungseinstellung festgelegt und unabhängig von der Geschwindigkeit der Produktionslinie oder der Belichtungszeit. Mit anderen Worten: Die Bestrahlungsstärke an der Härtungsoberfläche nimmt mit zunehmender Lampenleistung zu und mit abnehmender Lampenleistung ab. Der Wert dieser Bestrahlungsstärke bleibt an der Härtungsoberfläche unabhängig von der Liniengeschwindigkeit konstant, vorausgesetzt, dass sich die Einstellung der Lampenleistung und der Abstand nicht ändern.
Bei UV-LED-Härtungssystemen für Flachglas und Quecksilberdampflampen mit Flutprofilen wird die Bestrahlungsstärke durch den Abstand zwischen jedem Punkt auf der Härtungsoberfläche und dem Lampenkopf beeinflusst. In beiden Fällen führen größere Abstände zu geringeren Bestrahlungsstärken an der Härtungsoberfläche. Dies liegt daran, dass die Strahlen des abgestrahlten Lichts sich ausbreiten oder voneinander abweichen, je weiter sie sich von der emittierenden Quelle entfernen. Dadurch verringert sich die Lichtkonzentration und die Bestrahlungsstärke. Bei fokussierten Quecksilberdampflampen ist die Bestrahlungsstärke bei der Brennweite am größten und nimmt ab, wenn die Härtungsoberfläche innerhalb oder außerhalb der Brennweite bewegt wird. Der Zweck einer fokussierten Quecksilberdampflampe besteht darin, den Großteil der abgestrahlten UV-Energie auf ein schmales Band zu konzentrieren, um die absolute Stärke der Bestrahlungsstärke zu erhöhen.
In Produktionssituationen sind die meisten Härtungsoberflächen dynamischer Bestrahlung ausgesetzt. Eine dynamische Bestrahlungsstärke entsteht, wenn ein Lampenkopf ohne Pause über eine Aushärtungsoberfläche fährt oder wenn eine Aushärtungsoberfläche ohne Pause unter einem Lampenkopf hindurchläuft. Wenn sich Punktpositionen auf der Härtungsoberfläche einer UV-Quelle nähern, sich ihr gegenüberstellen oder sich von ihr entfernen, variiert die entsprechende Spitzenbestrahlungsstärke, die an jeder Position und zu jedem Zeitpunkt einfällt.
Ein dynamisches Bestrahlungsstärkeprofil kann viele Formen annehmen, liegt jedoch im Allgemeinen in Form der Glockenkurve vor, die in der folgenden grafischen Abbildung dargestellt ist. In der Grafik erfasst jeder Punkt des Bestrahlungsstärkeprofils die Spitzenbestrahlungsstärke zu jedem Zeitpunkt, wobei die Spitze der Glockenkurve den Moment darstellt, in dem die ausgehärtete Oberfläche durch den Brennpunkt einer Quecksilberdampflampe oder durch die Mitte einer UV-Strahlung verläuft LED-Lampe. Quellen mit einer größeren Spitzenbestrahlungsstärke haben einen höheren Profilpeak. Quellen mit einer geringeren Spitzenbestrahlungsstärke haben ein kürzeres Spitzenprofil. Die Breite des Profils wird von der Breite des UV-Lampenkopfes sowie der Geschwindigkeit der Prozesslinie oder der Belichtungszeit bestimmt.

Energiedichte (J/cm2)
Die Energiedichte ist die gesamte Strahlungsenergie, die pro Flächeneinheit auf einer Oberfläche ankommt, und wird in J/cm2 oder mJ/cm2 ausgedrückt. Die Energiedichte ist die Integration der Bestrahlungsstärke (W/cm2 oder mW/cm2) über die Belichtungszeit. Dies wird durch die Fläche unter dem Bestrahlungsstärkeprofil dargestellt, wie im vorherigen Bild gezeigt. Die Belichtungszeit und damit die Energiedichte bzw. die Fläche unter der Kurve wird durch Verlangsamung der Liniengeschwindigkeit, Erhöhung der Verweilzeit, Hinzufügen zusätzlicher Härtungsquellen oder Verwendung breiterer Köpfe bei UV-LEDs erhöht. Grafisch gesehen verteilen diese Aktionen die Breite der glockenförmigen Kurve über einen längeren Zeitraum, glätten den Peak oder erzeugen mehrere deutliche Peaks, wenn mehrere Lampenköpfe in Reihe verwendet werden.
Sobald bei einer bestimmten Aushärtungsanwendung die richtige spektrale Leistung und die richtige Mindestschwellenbestrahlungsstärke auf die Aushärtungsoberfläche aufgebracht werden, ist die Energiedichte der kritischste Faktor, der sich auf die Geschwindigkeit und den Grad der Aushärtung auswirkt. Während die Bestrahlungsstärke die Geschwindigkeit der Energieübertragung oder Leistung angibt, ist die Energiedichte die insgesamt abgegebene Energie. UV-Härtungsquellen, die eine höhere Energiedichte bieten, ermöglichen eine Härtung bei schnelleren Liniengeschwindigkeiten als Härtungssysteme mit niedrigeren Energiedichten.
Obwohl dies technisch nicht korrekt ist, wird die Energiedichte üblicherweise als Dosis bezeichnet, und wann immer von Dosis die Rede ist, wird darunter im Allgemeinen die Energiedichte verstanden. Der Klarheit halber ist die Energiedichte die abgegebene Energie, während die Dosis die absorbierte Energie ist. Die absorbierte Energie ist in der Praxis äußerst schwer zu quantifizieren. wohingegen die Energiedichte mithilfe von UV-Radiometern und Energiedichte-Teststreifen angenähert werden kann. Es ist immer wichtig, das Messgerät und die Leitungsgeschwindigkeit zu beachten, wenn mit Radiometern ermittelte Energiedichtewerte gemeldet werden.
UV-Härtungschemie und Photopolymerisation
Die chemischen Reaktionen der UV-Härtung beruhen auf Photoinitiatoren, die in speziell formulierten Tinten, Beschichtungen, Klebstoffen und Extrusionen dispergiert sind. Wenn Photoinitiatoren Lichtwellenlängen zwischen 100 und 450 nm ausgesetzt werden, absorbieren sie UV-Energie und erzeugen entweder freie Radikale oder kationische Spezies. Die angeregten Spezies treiben Reaktionen durch Initiierung, Ausbreitung und Beendigung voran, wodurch sich die molekulare Struktur der Rohstoffkomponenten schnell verändert. Bei UV-Härtungsanwendungen kommen vorwiegend radikalische Härtungsmechanismen zum Einsatz, während kationische Anwendungen nur wenige Prozent aller UV-härtbaren Chemikalien ausmachen.
Bei der Aushärtung durch freie Radikale entstehen freie Radikale, die Vernetzungsreaktionen vorantreiben. Um die Aushärtung durch freie Radikale einzuleiten und auszubreiten, ist eine kontinuierliche und direkte UV-Bestrahlung in Sichtlinie erforderlich. Reaktionen enden im Bruchteil einer Sekunde schnell und führen zu neuen Materialformen mit wünschenswerten Eigenschaften. Die Chemie freier Radikale kann insbesondere an der Härtungsoberfläche anfällig für Sauerstoff sein. Sauerstoffmoleküle entziehen dem Aushärtungsprozess freie Radikale und/oder verringern die Stärke freier Radikale. Die Erhöhung der Lampenbestrahlungsstärke, die Aushärtung in einer Stickstoffumgebung und die Veränderung der Chemie sind weit verbreitete Mittel, um der Sauerstoffhemmung entgegenzuwirken.
Ein alternativer und weniger genutzter Härtungsmechanismus ist die kationische Härtung. Diese Reaktion erzeugt Kationen, die die Vernetzung vorantreiben. Bei der kationischen Härtung ist zum Einleiten der Aushärtung eine UV-Bestrahlung erforderlich, die Ausbreitung erfolgt jedoch ohne kontinuierliche oder vollständige UV-Bestrahlung mit direkter Sichtlinie. Abhängig von der Chemie und der Anwendung breiten sich kationische Härtungsprozesse über Minuten, Stunden oder sogar Tage aus, bevor sie vollständig beendet werden. Die kationische Chemie reagiert empfindlich auf Feuchtigkeit und Temperatur, die beide die Vernetzung beeinträchtigen können. Daher sollten die Umgebungsbedingungen bei jedem Einsatz kationischer Chemie überwacht und kontrolliert werden.
UV-härtbare Formulierungen, ob freiradikalisch oder kationisch, werden aus im Handel erhältlichen Materialien formuliert. Obwohl die Auswahl recht vielfältig ist, sind die meisten Rohstoffe nach den folgenden Typen gruppiert.
- Photoinitiatoren – Moleküle, die ultraviolette Energie über einen definierten Wellenlängenbereich absorbieren und photopolymere Reaktionen durch die Bildung freier Radikale oder Kationen antreiben. Photoinitiatoren machen 0,5 bis 15 Gew.-% der gesamten UV-Formulierung aus.
- Monomere – Arten von Harzmolekülen mit relativ niedrigem Molekulargewicht und einfacher Struktur, die sich mit sich selbst oder anderen ähnlichen Molekülen verbinden können, um UV-vernetzte Polymere zu bilden. Monomere sind reaktive Verdünner, die zur Einstellung der Gesamtviskosität und zur Beeinflussung der Eigenschaften des ausgehärteten Materials verwendet werden. Monomere können bis zu 50 % des Gesamtgewichts der Formulierung ausmachen und können in seltenen Fällen teilweise oder vollständig durch Wasser oder Lösungsmittel ersetzt werden.
- Oligomere – Arten von Harzmolekülen mit relativ niedrigem Molekulargewicht und einfacher Struktur, die in der Lage sind, sich mit sich selbst oder anderen ähnlichen Molekülen zu verbinden, um UV-vernetzte Polymere zu bilden. Oligomere bilden das Rückgrat vernetzter Materialien, beeinflussen viele Eigenschaften des ausgehärteten Materials und machen zwischen 50 und 80 % des Gewichts der Formulierung aus.
- Additive – alle anderen Komponenten, die hinzugefügt werden, um die Eigenschaften der Mischung vor dem Aushärten sowie die Eigenschaften des Polymers nach dem Aushärten zu optimieren. Zu den Additiven gehören unter anderem Fließmodifikatoren, Entschäumer, Dispergiermittel und Lichtstabilisatoren. Additive stellen neben Pigmenten den kleinsten Anteil der gesamten UV-Mischung dar.
- Pigmente – spezifische Arten von Zusatzstoffen, die Formulierungen Farbe verleihen.
Photoinitiatoren, Monomere, Oligomere, Additive und manchmal auch Pigmente werden von Chemikern gemischt, um UV-härtbare Tinten, Beschichtungen, Klebstoffe und Extrusionen zu bilden. Freie Radikale oder kationische Spezies werden innerhalb der Chemie erzeugt, wenn sie einer optimalen Kombination aus UV-Wellenlänge (nm) und Bestrahlungsstärke (W/cm2) ausgesetzt werden. Die Photopolymerisation erfolgt sehr schnell, wobei die Verarbeitungszeiten nur Bruchteile einer Sekunde betragen. Der genaue Zeitpunkt und die Fähigkeit der Mischung zur geeigneten Vernetzung hängen von der Mischung der Rohstoffe ab; die spektrale Leistung (nm), die Bestrahlungsstärke (W/cm2) und die Energiedichte (J/cm2) der emittierenden Quelle; der Antrag; die Einrichtung der Produktionslinie; und die Verwendung von radikalischen oder kationischen Härtungsmechanismen. Die folgende Abbildung zeigt eine ungehärtete UV-Formulierung und die Vernetzung, die entsteht, wenn die Formulierung einer geeigneten UV-Energiequelle ausgesetzt wird.
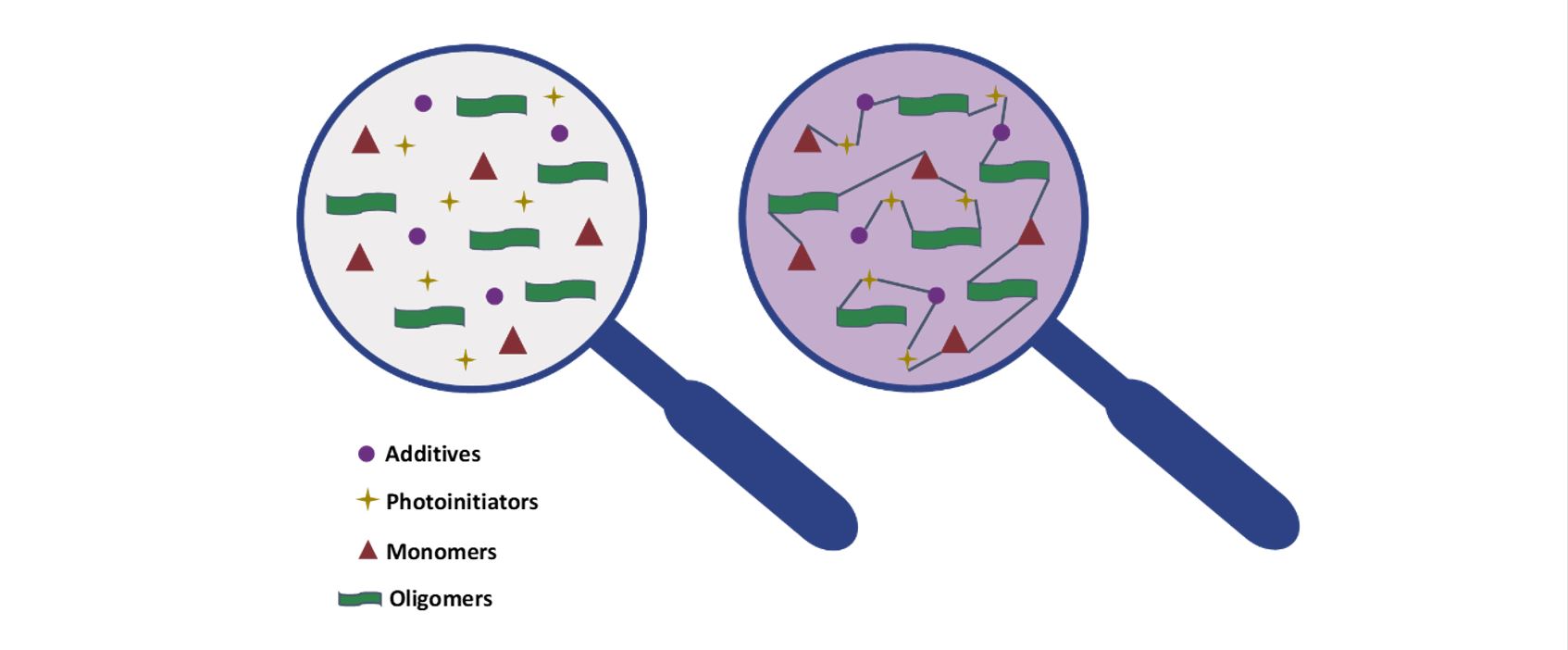
Aufgrund der flüssigkeitsähnlichen Beschaffenheit von UV-Formulierungen können die Materialien sowohl extrudiert als auch auf eine Vielzahl von Oberflächen und Materialien gesprüht, gespritzt, verteilt, gerollt, getaucht, gedruckt, gesputtert, abgesaugt oder geflutet werden. Nach der Anwendung genügt die Einwirkung ultravioletter Energie, um eine Ausbreitungs- und Vernetzungsreaktion auszulösen, die die Moleküle effizient und effektiv zu festen, homogenen Strukturen verbindet.
Prozess der UV-Härtung
Vernetzungsreaktionen, die während der UV-Härtung auftreten, sind nur ein Schritt in einer Reihe miteinander verbundener Herstellungsprozesse, die sowohl vor als auch nach der Härtung ablaufen. Alle Schritte sollten identifiziert, in den Prozess einbezogen, auf ihre gegenseitige Auswirkung hin bewertet und dann beibehalten werden, um konsistent Produkte herzustellen, die sowohl die Qualitäts- als auch die Endanwendungsleistungsanforderungen erfüllen.
Zu den Prozessschritten im Zusammenhang mit der UV-Härtung gehören häufig:
- Bewertung der Härtungsoberfläche – Form, Struktur, Materialart, Materialqualität, Oberflächenenergie und Sauberkeit der Härtungsoberfläche sind wichtig. Diese Aspekte bestimmen, ob eine Vorbehandlung notwendig ist; die entsprechende Tinten-, Beschichtungs- oder Klebstoffformulierung; die Materialhandhabung; und die notwendige Ausrichtung des UV-Lampenkopfes. Oberflächen sollten während der Prozessentwicklung bewertet und während der regulären Produktion regelmäßig bewertet werden.
- Vorbehandlung und Substratmodifikation – Teile- und Materialoberflächen müssen oft gereinigt, von statischer Aufladung befreit oder behandelt werden, um die Oberflächenenergie zu erhöhen. Diese Schritte sind häufig notwendig, um die Benetzung von Tinten, Beschichtungen und Klebstoffen zu erleichtern und die Haftung zu verbessern. Zu den Behandlungen gehören Waschen; chemische Bäder oder Tücher; antistatische Geräte; das Auftragen von Grundierungen, Grundanstrichen oder Leimungen; Flamme; Corona; Plasma; Schleifen; und Sandstrahlen unter anderem.
- Materialhandhabung – Materialoberflächen werden typischerweise als Platten, Bahnen oder dreidimensionale Teile durch Produktionsanlagen geführt. Die Materialhandhabung muss es ermöglichen, dass Tinte, Beschichtung oder Klebstoff gleichmäßig auf die Materialoberfläche aufgetragen und dann in einem definierten Versatzabstand zum Lampenkopf einer UV-Quelle ausgesetzt werden.
- Tinten-, Beschichtungs- oder Klebstoffformulierung – Die Anwendung, die Materialoberfläche, die Art der Formulierungsabgabe, das Härtungssystem und seine UV-Leistung, die Liniengeschwindigkeit oder Zyklusrate sowie die endgültigen Verwendungsanforderungen bestimmen alle die erforderlichen Eigenschaften der Formulierung. Es ist wichtig, diese Details mit den Formulierungsanbietern zu teilen, um sicherzustellen, dass optimale Formulierungen verwendet werden.
- Ausrüstung zur Formulierungsabgabe – Tinten, Beschichtungen und Klebstoffe können während des Produktionsprozesses auf verschiedene Arten aufgetragen werden, beispielsweise durch Sprühen, Spritzen, Dosieren, Rollen, Tauchen, Übertragen, Sputtern, Vakuumieren oder Überfluten. Die Auftragsgeräte sollten auf die Formulierung, die Art des auszuhärtenden Teils sowie das Material, aus dem es besteht, und seine Form oder sein Profil abgestimmt sein. Auch die Geschwindigkeit der Prozesslinie spielt eine Rolle, da sie die erforderliche Energiedichte bestimmt.
- Verdunstung flüssiger Träger – Eine kleine Liste von UV-Formulierungen enthält auch Wasser oder Lösungsmittelträger, die vor der Einwirkung von ultraviolettem Licht verdampft werden müssen. In manchen Fällen reicht die Dauer des Transports des Teils zur Aushärtungsquelle aus, damit die Verdunstung stattfinden kann, und in anderen Fällen muss ein Trocknungsmechanismus in den Prozess integriert werden, um die Verdunstung zu beschleunigen.
- UV-Härtung – Die Chemie freier Radikale erfordert direkte UV-Strahlung, UV-Wellenlängen, die auf die Photoinitiatoren in der Formulierung abgestimmt sind, eine Mindestbestrahlungsschwelle, die dem Abstand der Lampe von der Härtungsoberfläche Rechnung trägt, und eine ausreichende Energiedichte, um an der gewünschten Linie auszuhärten Geschwindigkeit. In vielen Anwendungen ist für jede aufgetragene Tinte, Beschichtung und jeden aufgetragenen Klebstoff ein eigenes UV-Härtungssystem erforderlich. Bei anderen Anwendungen können mehrere Formulierungen gleichzeitig mit einer einzigen Lampenkopfbelichtung ausgehärtet werden.
- Zusätzliche Prozessausrüstung – Viele UV-Härtungsanwendungen erfordern andere Ausrüstung, um die Aushärtung zu unterstützen oder die Prozessbedingungen zu verwalten. Dazu gehören Stickstoffinertisierungssysteme, Kühlwalzen oder Kühlplatten, zwangsgespülte oder unter Druck stehende Lampenköpfe oder Härtungskammern, Reinräume, externe Optiken, UV-Filter und integrierte UV-Messsysteme.
- Nachbehandlung nach dem Aushärten – Sobald das Teil oder die Materialoberfläche ausgehärtet ist, ist häufig eine Bearbeitung, Endbearbeitung, Montage, Befüllung, Verpackung und Versand erforderlich.
- Qualitätsprüfungen – Jede Anwendung hat unterschiedliche Qualitäts- und Leistungsanforderungen. Manchmal gehört dazu auch die Farbanpassung. In anderen Fällen könnten es eher funktionale Merkmale sein. Es sollten Prozesse eingerichtet werden, die quantifizierbare Ziele liefern, die während der Produktion regelmäßig überwacht werden können, wobei die Prozessvariablen bei Bedarf korrigiert werden können.
- Endanwendungsleistung – Die Verwendungsbedingungen für das Endprodukt sind äußerst wichtig für die Bestimmung aller vorangehenden Prozessschritte in dieser Liste. Es ist wichtig, mit allen prozessbezogenen Anbietern Gespräche über die Endverwendung zu führen.
- Qualifikationen, Genehmigungen und Zertifizierungen – Die verarbeiteten und UV-gehärteten Artikel werden letztendlich an eine andere Partei geliefert, die möglicherweise spezifische Anforderungen hat, die bestimmen, ob der gesamte Produktionsprozess für ihre Bedürfnisse oder Unternehmensziele geeignet ist. Das Einholen geeigneter Qualifikationen, Genehmigungen und Zertifizierungen vom Käufer und die anschließende Führung geeigneter Prüfprotokolle ist oft ein entscheidender Schritt.
Während die bereitgestellte Aufzählungsliste einen soliden Überblick über einen UV-Härtungsprozess darstellt, handelt es sich nicht unbedingt um eine vollständig umfassende Liste aller möglichen Aktivitäten. Jede UV-Härtungsanwendung und jede UV-Fertigungslinie weist einzigartige Eigenschaften auf, die zu Prozessschritten führen können, die nicht aufgeführt sind. In jedem Fall ist es immer wichtig, UV-Härtungsanwendungen, die Fertigungslinie, in die der Prozess integriert werden soll, die Verarbeitungsaktivitäten nach der Härtung und die Verwendung des Endprodukts als vollständigen Prozess zu bewerten, bei dem jeder Schritt möglicherweise Auswirkungen auf andere Schritte hat. Glücklicherweise ist ein einmal etablierter UV-Härtungsprozess unglaublich zuverlässig, wiederholbar und kontrollierbar.
Insgesamt ermöglicht die UV-Härtung den Herstellern die Herstellung von Produkten mit höchst wünschenswerten physikalischen, mechanischen und ästhetisch ansprechenden Eigenschaften, die letztendlich das Gesamterscheinungsbild, die Qualität und die Leistung zahlreicher Alltagsgegenstände verbessern. Das Verständnis der Grundlagen der UV-Härtung, der Lichtwissenschaft, der UV-Chemie und der Prozessvariablen erleichtert die optimale Auswahl der UV-Härtungsquelle und -Formulierung, die richtige Integration, Prozesskontrolle und die konsistente Produktion von Qualitätsprodukten.